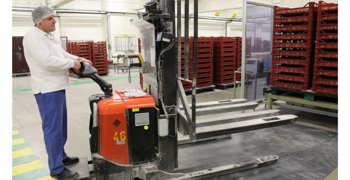
-
- Témoignages clients
-
Astra Sweets réduit ses coûts grâce à des camions peseurs
Le fabricant de bonbons Astra Sweets ne connaissait auparavant pas le poids exact de chaque cycle de production. Cela entraînait des restes, des retards de livraison ou des cycles correctifs coûteux. L'entreprise cherchait une solution à ce problème.
analyse de rentabilité
Bonbons Astra
Dans son usine principale de Turnhout, l'entreprise belge produit 300 sortes de bonbons. Toutes ces confiseries sont distribuées sous sa propre marque dans les supermarchés, les drogueries, les stations-service et chez les grossistes, ou sous marque de distributeur à un large champ de clients importants en Belgique et à l'étranger. Quiconque visite le département production d'Astra Sweets voit des bonbons aux couleurs vives sortir des machines. Les bonbons sont empilés dans des plateaux par des robots, puis transportés sur des palettes par des chariots vers l'entrepôt intermédiaire.
Patrick Peeters, Key User Production, explique : « Nos bonbons sont versés dans des moules en amidon. Ils passent ensuite dans une salle de séchage ou de réfrigération. La touche finale est apportée après 36 heures. Le produit semi-fini est ensuite placé dans des plateaux. Ceux-ci sont transportés sur des palettes vers l'entrepôt intermédiaire où, après acclimatation, les bonbons sont finalement emballés selon la commande du client. »
Situation actuelle
La gestion des stocks tampons pouvait être améliorée, explique Stefan Verbeken, responsable de la planification et de l'approvisionnement en matériaux chez Astra Sweets. « Nous produisons sur trois lignes de moulage. Chaque processus de production comporte des pertes au démarrage. Ajoutez à cela les pannes pendant le cycle et vous comprenez pourquoi la sortie réelle peut différer considérablement de la sortie théorique attendue. Nous connaissions bien sûr les quantités de matières premières utilisées, mais nous ne pouvions pas mesurer le rendement exact à la fin de la chaîne. Nous ne pouvions donc pas savoir avec certitude quelle quantité de produits semi-finis se trouvait dans l'entrepôt tampon. Les écarts entre les stocks enregistrés dans notre ERP et ceux de notre entrepôt pouvaient atteindre plusieurs tonnes, selon la taille du lot produit. »
Les incertitudes liées aux stocks tampons de produits semi-finis entraînaient des inefficacités et des coûts supplémentaires. Afin de limiter au maximum les changements de produits sur les lignes, toutes les commandes des clients, par exemple pour les bouteilles de cola, sont regroupées dans un seul cycle de production, puis produites et transportées vers l'entrepôt tampon. « Si un produit semi-fini était prévu pour plusieurs commandes d'emballage, cela était basé sur le rendement théorique, avec le risque que certaines commandes soient trop ou pas assez emballées. Cela entraînait des changements de dernière minute dans la planification de la production afin d'éviter des problèmes de livraison. Les changements supplémentaires dans les cycles d'emballage et les petits cycles de coulée correctifs ajoutaient des coûts inutiles. À un moment donné, nous avons commencé à faire des inventaires quotidiens dans l'entrepôt tampon pour éviter cela, ce qui nous a coûté beaucoup d'heures de travail. »
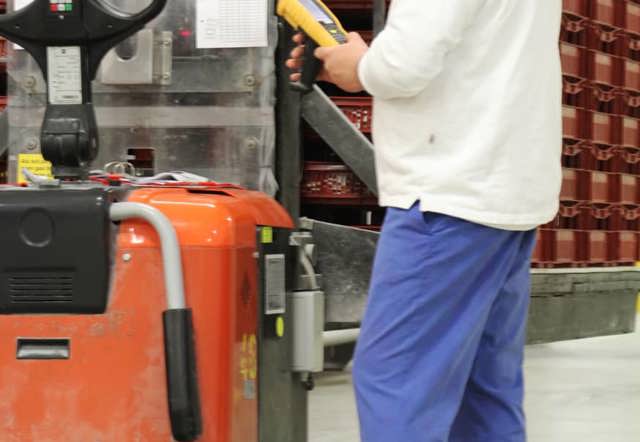
Investissements en matériel et logiciels
Astra Sweets a investi dans quatre systèmes de pesage avec WiFi, deux RCS Hy-Q sur des gerbeurs à double fourche et deux RPW EL sur des transpalettes électriques.
Comment ça marche ?
Un projet d'amélioration a été lancé : tous les bonbons sortant des chaînes de production devaient être pesés. Plusieurs options ont été envisagées : l'intégration de systèmes de pesage dans les lignes de production s'est avérée coûteuse, le pesage sur une balance au sol était chronophage et pas toujours sûr en raison des goulots d'étranglement logistiques dans le trafic interne. Patrick Peeters avait déjà utilisé RAVAS chez un ancien employeur et a suggéré d'installer des systèmes de pesage mobiles sur les chariots élévateurs qui assurent le transport interne depuis les lignes de production vers l'entrepôt intermédiaire. Stefan Verbeken : « Cela s'est avéré être la solution la plus efficace et la plus rentable. »
Une demande d'investissement a été introduite, accompagnée d'une analyse coûts-bénéfices. Les coûts comprenaient quatre systèmes de pesage, mais aussi le remplacement de deux anciens chariots, car selon Astra Sweets, il aurait été absurde d'intégrer un système de pesage dans des chariots qui n'avaient plus que quelques années de vie utile. À cela s'ajoutaient les coûts de modification du logiciel Objective qui contrôle les lignes de production. Les avantages l'emportaient largement sur les inconvénients. Un demi-ETP a pu être économisé immédiatement sur les contrôles quotidiens dans l'entrepôt et toutes sortes de corrections dans l'emballage. À cela s'ajoutent : un emballage dans le bon ordre, moins de résidus et de déchets et moins de coulées correctives.
Patrick Peeters décrit le processus actuel : « Nous disposons désormais de quatre chariots équipés de systèmes de pesage. Le système de pesage et le terminal portable sur le chariot communiquent via notre réseau WLAN avec Objective. Lorsque le produit semi-fini sort de la ligne de production, il est immédiatement pesé sur le chariot. L'opérateur lance le protocole sur son terminal portable : il introduit le numéro de la chaîne de production et l'article concerné. Il déclenche ensuite Objective pour demander le poids au système de pesage sur le chariot, et le jeu de données est complet. Une étiquette avec un code-barres est imprimée à partir du terminal portable et la palette est envoyée à l'entrepôt intermédiaire. »
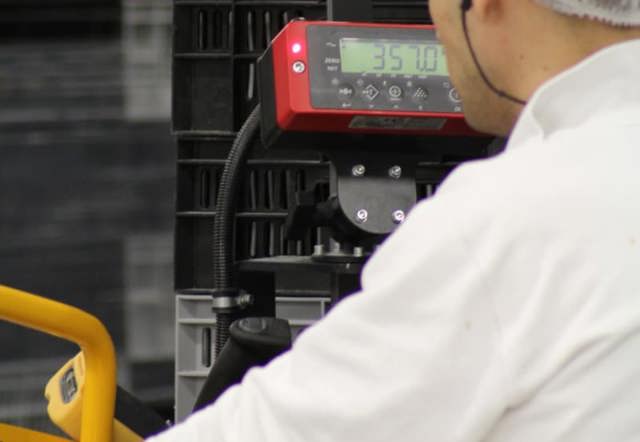
Stefan Verbeken, Responsable Planification et Approvisionnement en Matériaux
« À un moment donné, nous avons commencé à faire des inventaires quotidiens pour contrer le problème. Cela nous coûtait de la main-d'œuvre que nous aurions pu utiliser à meilleur escient ailleurs. Grâce aux balances mobiles RAVAS, nous générons désormais des chiffres réels et pouvons gérer nos activités à l'aide d'indicateurs clés de performance. Cela nous a permis de réaliser immédiatement des économies, et l'investissement dans les systèmes de pesage a été rapidement amorti. »
Résultats
Patrick Peeters : « L'avantage de l'intégration entre les systèmes de pesage et Objective est que nous pouvons désormais comparer les lignes et voir les résultats des systèmes de pesage. Nous n'avons que 50 kg de corrections par mois, ce qui est extrêmement faible par rapport à notre tonnage mensuel. »
Stefan Verbeken : « Les données sont transmises d'Objective à SAP. Nous disposons désormais de données réelles après la production. Nous pouvons également effectuer des analyses de rendement par produit et optimiser à partir de là. Nous pouvons nous baser sur des indicateurs clés de performance. La planification de l'emballage peut désormais être mieux adaptée aux besoins du client. Grâce aux systèmes de pesage mobiles RAVAS, nous avons fait un pas en avant dans notre processus de production. »
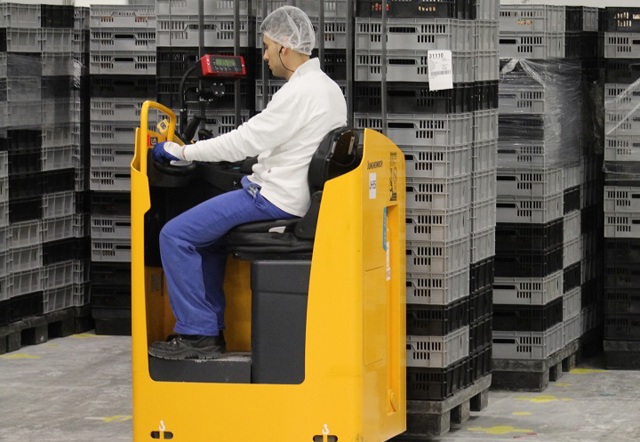
À propos de l'application
Contrôle des stocks
Avec des chaînes d'approvisionnement mondiales qui s'étendent sur plusieurs continents, des stocks réduits et des livraisons juste à temps, les entreprises sont devenues très vulnérables aux ruptures de stock. Les ruptures de stock entraînent des interruptions des processus de production, des retards et une perte de confiance des clients. Et tout cela a un coût. Grâce à une balance mobile connectée à votre système ERP ou WMS, vous pouvez surveiller les flux de matériaux à chaque fois que des marchandises sont déplacées : marchandises entrantes, marchandises en cours de production, marchandises sortantes. Sans interrompre le processus, les balances mobiles vous permettent de contrôler avec précision vos stocks, de réduire les niveaux de stock et de diminuer les coûts.
Produits adaptés
Pour le contrôle des stocks
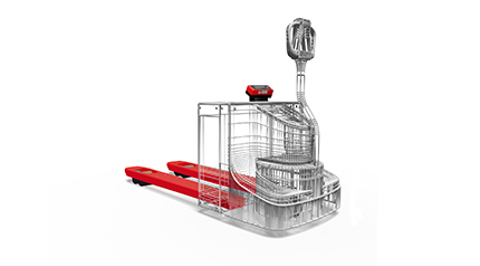
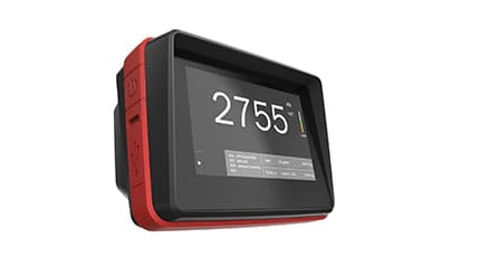
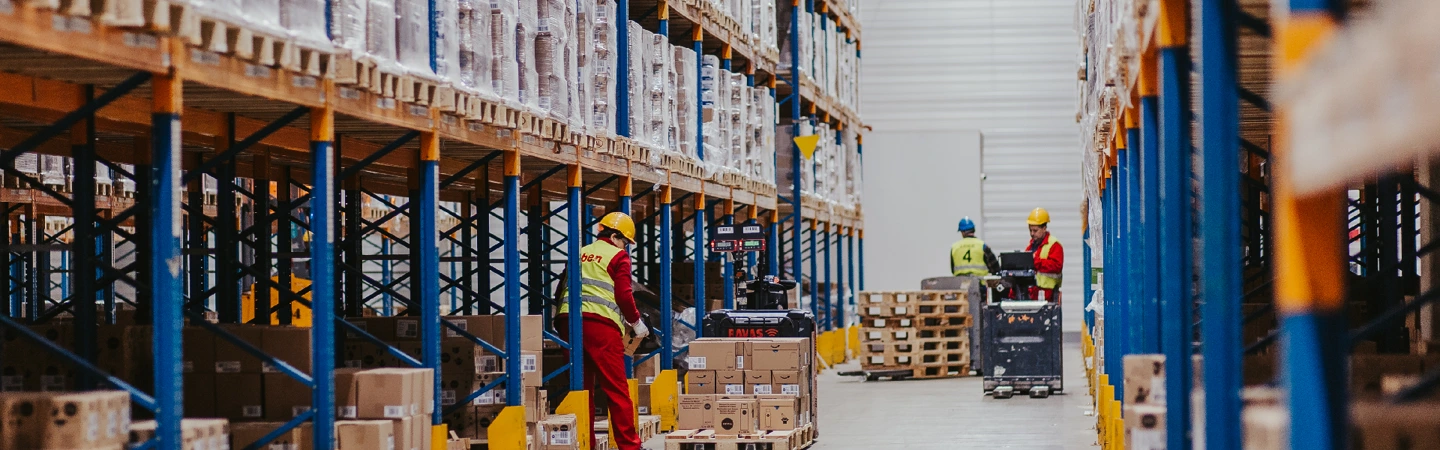