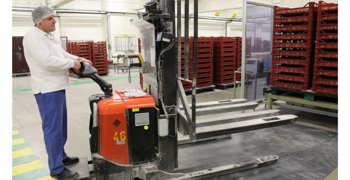
-
- Casos de éxito
-
Astra Sweets ahorra costes inmediatamente con los camiones con báscula
El fabricante de caramelos Astra Sweets no sabía anteriormente el peso exacto por ciclo de producción. Esto provocaba residuos, retrasos en las entregas o costosas tiradas correctivas.
Caso de negocio
Dulces Astra
En su planta principal de Turnhout, la empresa belga produce 300 tipos diferentes de dulces. Todos estos productos de confitería se distribuyen con su propia marca a supermercados, droguerías, gasolineras y mayoristas, o con marcas blancas a una amplia gama de clientes importantes en Bélgica y en el extranjero. Cualquiera que visite el departamento de producción de Astra Sweets verá dulces de alegres colores saliendo de las máquinas. Los dulces son apilados en bandejas por robots y transportados en palets por camiones al almacén intermedio.
Patrick Peeters, usuario clave de producción, explica: «Nuestros caramelos se vierten en moldes de almidón. A continuación, pasan a una sala de secado o refrigeración. Los toques finales se aplican tras 36 horas. El producto semiacabado se vierte en bandejas. Estas se colocan en palets que se envían al almacén intermedio, donde, tras la aclimatación, los dulces se envasan finalmente según el pedido del cliente».
Situación actual
La gestión del stock de amortiguación dejaba margen de mejora, afirma Stefan Verbeken, director de Planificación y Suministro de Materiales de Astra Sweets. «Producimos en tres líneas de fundición. Cada proceso de producción tiene sus pérdidas iniciales. Si a esto le sumamos los fallos durante el funcionamiento, es fácil comprender por qué la salida real puede diferir significativamente de la salida teórica esperada. Por supuesto, conocíamos la cantidad de materia prima utilizada, pero no podíamos medir el rendimiento exacto al final de la línea. Por lo tanto, no podíamos estar seguros de la cantidad de productos semiacabados que había en el almacén de reserva. Las discrepancias entre el stock de nuestro ERP y el stock de nuestro almacén podían ascender a varias toneladas, dependiendo del tamaño de la tirada de producción».
Las incertidumbres en las existencias de productos semiacabados en el almacén intermedio provocaban ineficiencias y costes adicionales. Para reducir al mínimo los cambios de producto en las líneas, todos los pedidos de los clientes, por ejemplo, botellas de cola, se agrupan en una sola tirada de producción, se fabrican y luego se transportan al almacén intermedio. «Si se planificaba un producto semiacabado para varios pedidos de envasado, esto se basaba en el rendimiento teórico, con el riesgo de que se envasara demasiado para algunos pedidos y demasiado poco para otros. Esto provocaba cambios de última hora en la planificación de la producción para evitar problemas de entrega. Los cambios adicionales en las tiradas de envasado y las pequeñas tiradas de fundición correctivas añadían costes innecesarios. En un momento dado, empezamos a hacer inventarios diarios en el almacén intermedio para evitarlo, lo que suponía muchas horas de trabajo».
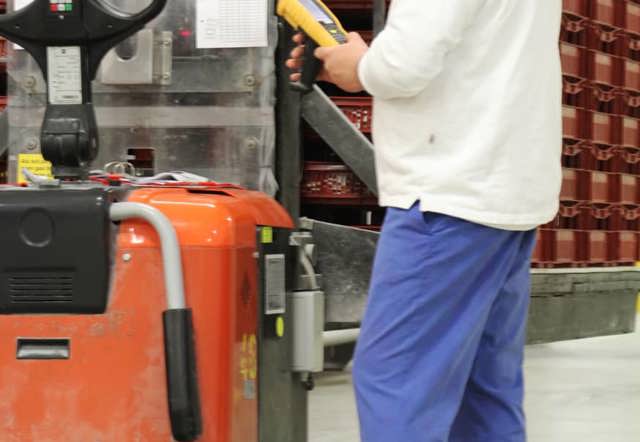
Inversión en hardware y software
Astra Sweets invirtió en cuatro sistemas de pesaje con WiFi, dos RCS Hy-Q en apiladores de doble horquilla y dos RPW EL en transpaletas eléctricas.
¿Cómo funciona?
Se inició un proyecto de mejora: todos los caramelos que salían de las líneas de producción debían pesarse. Se barajaron varias opciones: integrar sistemas de pesaje en las líneas de producción resultaba caro, y pesar en una báscula de suelo llevaba mucho tiempo y no siempre era seguro debido a los cuellos de botella logísticos en el tráfico interno. Patrick Peeters tenía experiencia con RAVAS en una empresa anterior y sugirió el pesaje móvil en las carretillas del almacén que se encargan del transporte interno desde las líneas de producción hasta el almacén intermedio. Stefan Verbeken: «Resultó ser la solución más eficiente y rentable».
Se inició una solicitud de inversión, respaldada por un análisis de costes y beneficios. Los costes consistían en cuatro sistemas de pesaje, pero también en la sustitución de dos carretillas más antiguas, ya que, según Astra Sweets, sería una destrucción de capital instalar un sistema de pesaje en carretillas que solo tenían unos pocos años de vida útil. A esto hay que añadir el coste de las modificaciones de Objective, el programa de software que controla las líneas de producción. Las ventajas superaban con creces los inconvenientes. Se pudo ahorrar inmediatamente medio ETC en los controles diarios del almacén y en todo tipo de correcciones en el embalaje. A esto hay que añadir el embalaje en el orden correcto, menos residuos y
desperdicios y menos tiradas de fundición correctivas.
Patrick Peeters describe el proceso actual: «Ahora tenemos cuatro camiones con sistemas de pesaje. Tanto el sistema de pesaje como el dispositivo portátil del camión se comunican a través de nuestra red WLAN con Objective. Cuando el producto semiacabado sale de la línea de producción, se pesa inmediatamente en el camión. El operario inicia el protocolo en su terminal portátil: introduce el número de la línea de producción y el artículo al que se refiere. A continuación, activa Objective para solicitar el peso al sistema de pesaje de la carretilla y, de este modo, se completa el conjunto de datos. Desde el terminal portátil se imprime una etiqueta con un codigo de barras y el palet se envía al almacén intermedio».
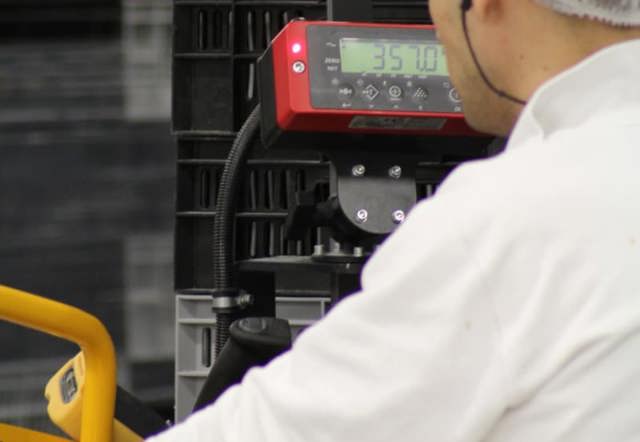
Stefan Verbeken, director de Planificación y Suministro de Materiales
«En un momento dado, empezamos a hacer inventarios diarios para contrarrestar el problema. Eso nos costaba mano de obra que podríamos haber utilizado de forma más rentable en otras tareas. Con las básculas móviles RAVAS, ahora generamos cifras reales y podemos gestionar los KPI. Esto supuso un ahorro inmediato de costes, y la inversión en los sistemas de pesaje se amortizó en poco tiempo».
Results
Patrick Peeters: "The advantage of the integration between the weighing systems and Objective is that we can now compare the lines and see the results of the weighing systems. We only have 50 kg corrections on a monthly basis - which is extremely low compared to our monthly tonnage."
Stefan Verbeken: "The data goes from Objective to SAP. We now have real data after production. We can also do yield analyses per product and optimise from there. We can steer on KPIs. Packing planning can now be tuned much better to the needs of the customer. With the help of the RAVAS mobile weighing systems we have made a step forward in our production process."
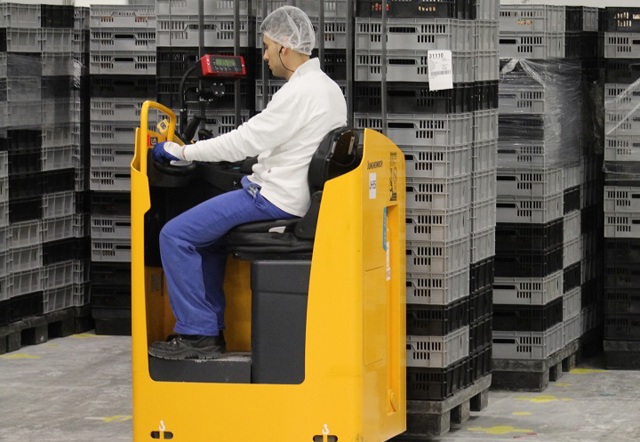
Acerca de la aplicación
Control de existencias
Con cadenas de suministro globales que se extienden por todos los continentes, con stocks reducidos y entregas justo a tiempo, las empresas se han vuelto muy vulnerables a la escasez de existencias. La escasez implica interrupciones en los procesos de producción, retrasos y pérdida de confianza de los clientes. Y todo ello tiene un coste. Con una báscula móvil conectada a su sistema ERP o WMS, se puede supervisar el flujo de materiales cada vez que se mueven las mercancías: mercancías entrantes, mercancías en producción y mercancías salientes. Sin interrumpir el proceso, las básculas móviles le permiten controlar con precisión sus existencias, reducir los niveles de stock y disminuir los costes.
Productos adecuados
Para el control de existencias
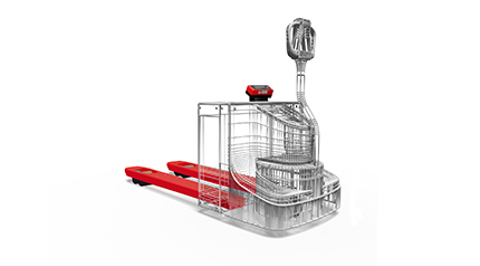
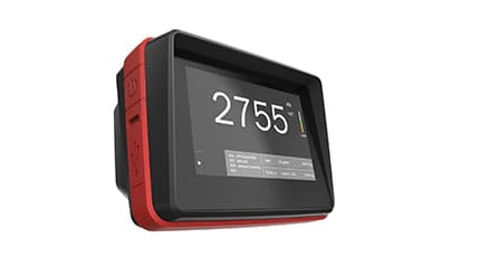
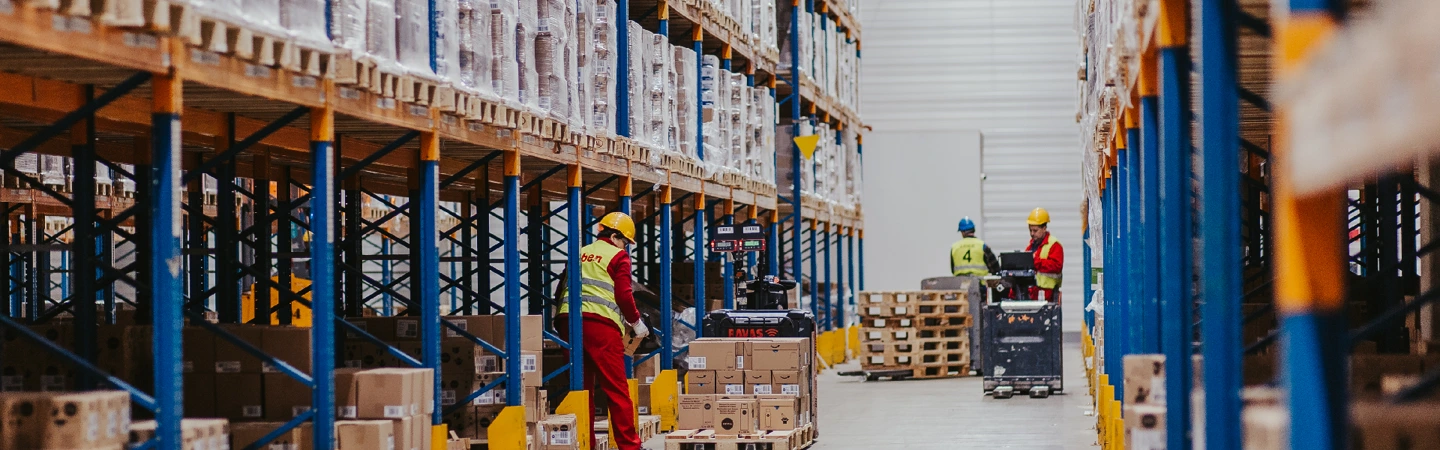