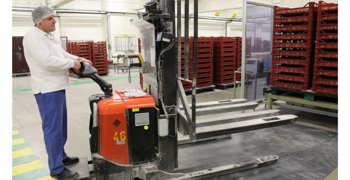
-
- Kundengeschichten
-
Astra Sweets spart sofort Kosten durch Wiege-LKWs
Der Süßwarenhersteller Astra Sweets kannte bisher das genaue Gewicht pro Produktionslauf nicht. Das führte zu Restmengen, Lieferverzögerungen oder teuren Nachbesserungen.
Geschäftsszenario
Astra Süßigkeiten
In seinem Hauptwerk in Turnhout produziert das belgische Unternehmen 300 verschiedene Süßwaren. Alle Süßwaren werden unter eigenem Markennamen an Supermärkte, Drogerien, Tankstellen und Großhändler oder unter Handelsmarken an eine Reihe von Großkunden im In- und Ausland vertrieben. Wer bei Astra Sweets durch die Produktion geführt wird, sieht bunte Süßigkeiten aus den Maschinen rollen. Die Süßigkeiten werden von Robotern in Trays gestapelt und mit Hubwagen auf Paletten zum Zwischenlager transportiert.
Patrick Peeters, Key User Production, erklärt: „Unsere Bonbons werden in Stärkegussformen gegossen. Anschließend kommen sie in einen Trockenraum oder in die Kühlung. Nach 36 Stunden erfolgt die Endbearbeitung. Das Halbfertigprodukt gelangt dann in Trays. Diese werden auf Paletten in das Zwischenlager gebracht, wo die Süßigkeiten nach der Akklimatisierung schließlich nach Kundenwunsch verpackt werden.“
Aktuelle Lage
Die Verwaltung der Pufferbestände war verbesserungswürdig, sagt Stefan Verbeken, Manager Planung und Materialversorgung bei Astra Sweets. „Wir produzieren auf drei Gießlinien. Jeder Produktionsprozess hat seine Anlaufverluste. Rechnet man Ausfälle während eines Laufs hinzu, wird klar, warum der tatsächliche Ausgang erheblich vom erwarteten, theoretischen Ausgang abweichen kann. Wir kannten natürlich den Rohstoffverbrauch, aber wir konnten die genaue Ausbeute am Ende der Linie nicht messen. Daher konnten wir nicht sicher sein, wie viel von einem Halbzeug im Pufferlager vorrätig war. Die Abweichungen zwischen dem Bestand in unserem ERP-System und dem Bestand in unserem Lager konnten je nach Größe der Produktionscharge mehrere Tonnen betragen.“
Die Unsicherheiten bei den produzierten Pufferbeständen an Halbfertigprodukten führten zu Ineffizienzen und zusätzlichen Kosten. Um Produktwechsel an den Fertigungslinien auf ein Minimum zu reduzieren, werden alle Kundenaufträge, z. B. für Colaflaschen, in einem einzigen Produktionslauf zusammengefasst, produziert und dann zum Pufferlager transportiert. „Wenn ein Halbzeug für mehrere Verpackungsaufträge vorgesehen war, basierte dies auf der theoretischen Ausbeute, mit dem Risiko, dass für einige Aufträge zu viel und für andere zu wenig verpackt wurde. Dies führte zu kurzfristigen Änderungen in der Produktionsplanung, um Lieferprobleme zu vermeiden. Zusätzliche Umstellungen in den Verpackungsläufen und kleine Korrekturgüsse verursachten unnötige Kosten. Um dies zu vermeiden, haben wir irgendwann begonnen, täglich Inventuren im Pufferlager durchzuführen, was viel Arbeitszeit in Anspruch nahm.“
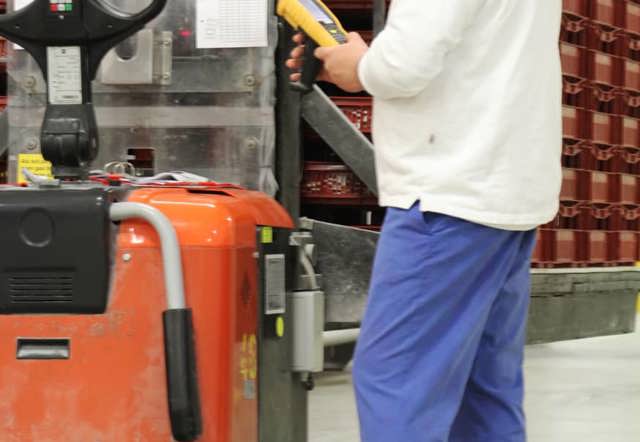
Investitionen in Hardware und Software
Astra Sweets investierte in vier Wiegesysteme mit WiFi, zwei RCS Hy-Q auf Doppelgabelstaplern und zwei RPW EL auf Elektrohubwagen.
Wie funktioniert das?
Ein Verbesserungsprojekt wurde ins Leben gerufen: Alle Süßigkeiten, die die Produktionslinien verließen, mussten gewogen werden. Es wurden mehrere Optionen in Betracht gezogen: Der Einbau von Wiegesystemen in die Produktionslinien erwies sich als kostspielig, das Wiegen auf einer Bodenwaage war zeitaufwändig und aufgrund logistischer Engpässe im internen Verkehr nicht immer sicher. Patrick Peeters hatte bei einem früheren Arbeitgeber Erfahrungen mit RAVAS gesammelt und schlug vor, mobile Wiegesysteme auf den Lagerfahrzeugen zu installieren, die den internen Transport von den Produktionslinien zum Zwischenlager übernehmen. Stefan Verbeken: „Das erwies sich als die effizienteste und kostengünstigste Lösung.“
Es wurde eine Investitionsanfrage mit einer Kosten-Nutzen-Analyse gestellt. Die Kosten umfassten vier Wiegesysteme, aber auch den Ersatz von zwei älteren Staplern, da es laut Astra Sweets Kapitalvernichtung gewesen wäre, ein Wiegesystem in Stapler einzubauen, die nur noch eine wenige Jahre Lebensdauer hatten. Hinzu kamen die Kosten für die Anpassung der Software „Objective“, mit der die Produktionslinien gesteuert werden. Die Vorteile überwogen jedoch bei weitem. Bei den täglichen Lagerkontrollen und allen möglichen Korrekturen beim Verpacken konnte sofort eine halbe Vollzeitstelle eingespart werden. Hinzu kommen: Verpackungen in der richtigen Reihenfolge, weniger Rückstände und Abfall sowie weniger Korrekturläufe.
Patrick Peeters beschreibt den aktuellen Prozess: „Wir haben jetzt vier Stapler mit Wiegesystemen. Sowohl das Wiegesystem als auch das Handheld auf dem Stapler kommunizieren über unser WLAN-Netzwerk mit Objective. Wenn das Halbfertigprodukt von der Produktionslinie kommt, wird es sofort auf dem Stapler gewogen. Der Bediener startet das Protokoll auf seinem Handheld: Er gibt die Nummer der Produktionslinie und den betreffenden Artikel ein. Anschließend fordert er über Objective das Gewicht vom Wiegesystem auf dem Hubwagen an, und schon ist der Datensatz vollständig. Über das Handheld wird ein Etikett mit Barcode gedruckt, und die Palette geht ins Zwischenlager.“
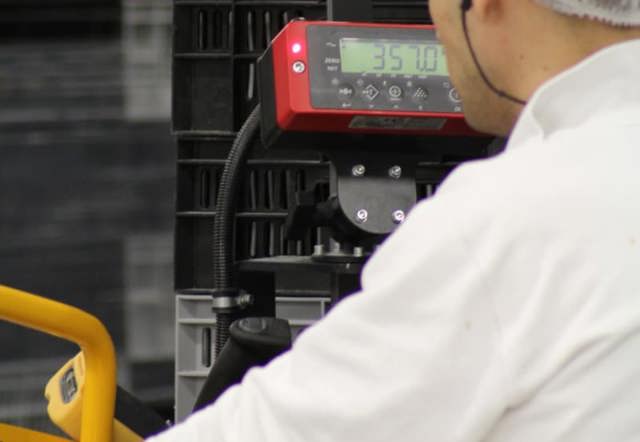
Stefan Verbeken, Leiter Planung und Materialversorgung
„An einem Punkt haben wir begonnen, täglich Inventuren durchzuführen, um dem Problem entgegenzuwirken. Das hat uns Arbeitskraft gekostet, die wir anderswo gewinnbringend hätten einsetzen können. Mit den mobilen Waagen von RAVAS generieren wir nun reale Zahlen und können anhand von KPIs arbeiten. Das hat sofort zu Kosteneinsparungen geführt, sodass sich die Investition in die Wiegesysteme in kurzer Zeit amortisiert hat.“
Ergebnisse
Patrick Peeters: „Der Vorteil der Integration zwischen den Wiegesystemen und Objective besteht darin, dass wir nun die Linien vergleichen und die Ergebnisse der Wiegesysteme sehen können. Wir haben nur noch 50 kg Korrekturen pro Monat – was im Vergleich zu unserer monatlichen Tonnage extrem wenig ist.“
Stefan Verbeken: „Die Daten werden von Objective an SAP weitergeleitet. Wir verfügen nun über reale Daten nach der Produktion. Wir können auch Ertragsanalysen pro Produkt durchführen und auf dieser Grundlage Optimierungen vornehmen. Wir können anhand von KPIs steuern. Die Verpackungsplanung lässt sich nun viel besser auf die Bedürfnisse der Kunden abstimmen. Mit Hilfe der mobilen Wiegesysteme von RAVAS haben wir einen Schritt nach vorne in unserem Produktionsprozess gemacht.“
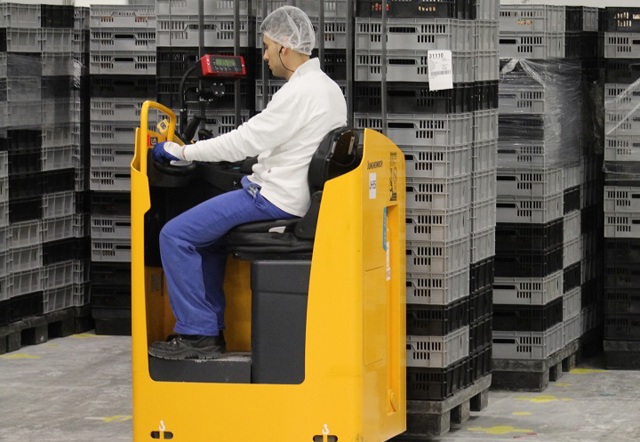
Über die Anwendung
Lagerverwaltung
Mit globalen Lieferketten, die sich über Kontinente erstrecken, mit kleinen Lagerbeständen und Just-in-Time-Lieferungen sind Unternehmen sehr anfällig für Lieferengpässe geworden. Engpässe bedeuten unterbrochene Produktionsprozesse, Verzögerungen und Verlust des Kundenvertrauens. Und all das verursacht Kosten. Mit einer mobilen Waage, die mit Ihrem ERP- oder WMS-System verbunden ist, können Materialflüsse bei jeder Warenbewegung überwacht werden: Wareneingang, Waren in der Produktion, Warenausgang. Ohne den Prozess zu unterbrechen, ermöglichen Ihnen mobile Waagen eine genaue Kontrolle Ihres Lagerbestands, eine Reduzierung der Lagerbestände und eine Senkung der Kosten.
Geeignete Produkte
Für die Lagerverwaltung
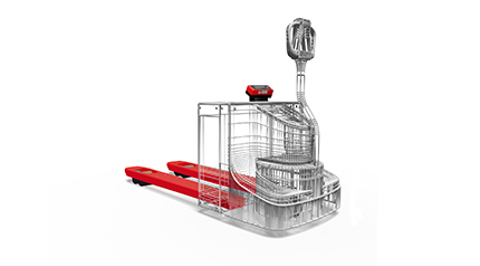
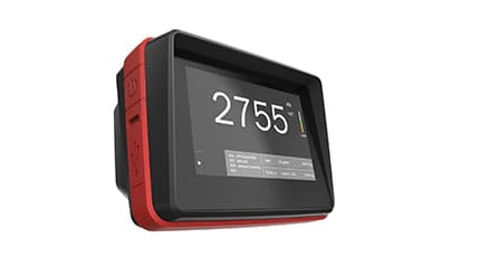
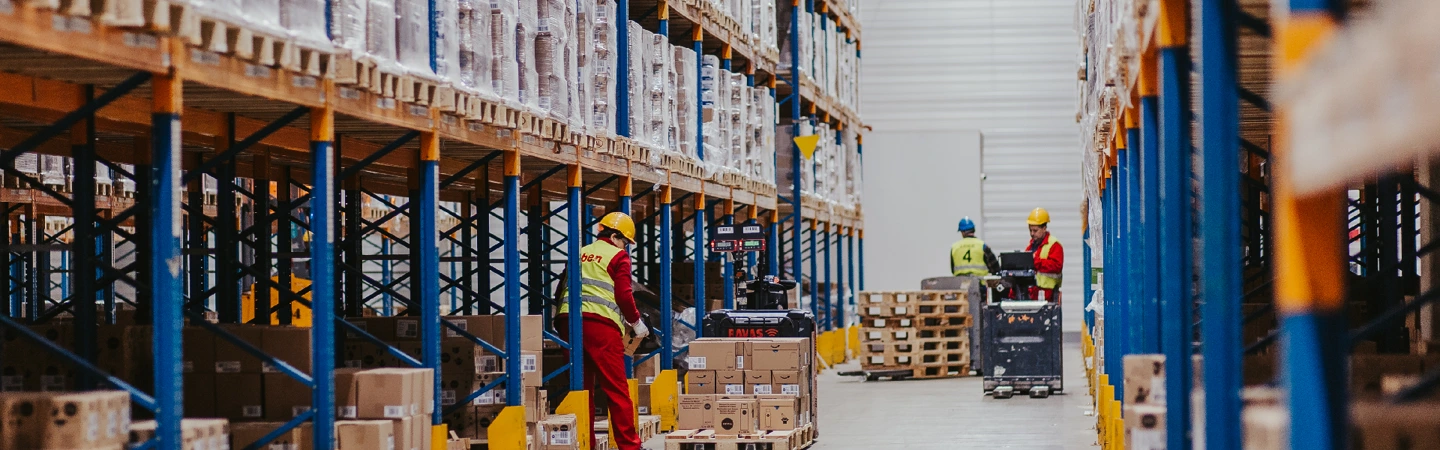