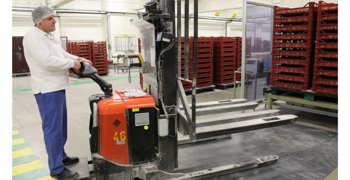
-
- Historie klientów
-
Astra Sweets natychmiast oszczędza koszty dzięki wózkom z wagą
Producent cukierków Astra Sweets nie znał wcześniej dokładnej masy poszczególnych partii produkcyjnych. Powodowało to powstawanie odpadów, opóźnienia dostaw lub kosztowne produkcje poprawkowe.
Analiza biznesowa
Słodycze Astra
W głównym zakładzie w Turnhout belgijska firma produkuje 300 różnych rodzajów słodyczy. Wszystkie wyroby cukiernicze są dystrybuowane pod własną marką do supermarketów, drogerii, stacji benzynowych i hurtowni lub pod marką własną do wielu dużych klientów w Belgii i za granicą. Każdy, kto zwiedza dział produkcji w Astra Sweets, może zobaczyć wesoło kolorowe cukierki wyjeżdżające z maszyn. Cukierki są układane w tackach przez roboty i transportowane na paletach ciężarówkami do magazynu przejściowego.
Patrick Peeters, główny użytkownik produkcji, wyjaśnia: „Nasze cukierki są wlewane do form skrobiowych. Następnie trafiają do suszarni lub chłodni. Ostatnie wykończenie następuje po 36 godzinach. Półprodukt trafia następnie na tace. Są one umieszczane na paletach i przewożone do magazynu pośredniego, gdzie po aklimatyzacji cukierki są ostatecznie pakowane zgodnie z zamówieniem klienta”.
Obecna sytuacja
Zarządzanie zapasami buforowymi wymagało poprawy, mówi Stefan Verbeken, kierownik ds. planowania i zaopatrzenia w firmie Astra Sweets. „Produkujemy na trzech liniach odlewniczych. Każdy proces produkcyjny wiąże się ze stratami początkowymi. Dodajmy do tego awarie podczas pracy i łatwo zrozumieć, dlaczego rzeczywiste wyj?cie może znacznie różnić się od oczekiwanego, teoretycznego wyj?cia. Oczywiście znaliśmy ilość surowców, ale nie byliśmy w stanie zmierzyć dokładnej wydajności na końcu linii. Dlatego nie mieliśmy pewności, ile półproduktów znajduje się w magazynie buforowym. Różnice między stanem magazynowym w naszym systemie ERP a stanem magazynowym w magazynie mogły sięgać kilku ton, w zależności od wielkości serii produkcyjnej”.
Niepewność co do wielkości zapasów buforowych półproduktów prowadziła do nieefektywności i dodatkowych kosztów. Aby ograniczyć do minimum zmiany produktów na liniach produkcyjnych, wszystkie zamówienia klientów, np. na butelki coli, są grupowane w jednym cyklu produkcyjnym, a następnie produkowane i transportowane do magazynu buforowego. „Jeśli półprodukt był planowany do wielu zamówień opakowań, opierano się na teoretycznej wydajności, co wiązało się z ryzykiem, że do niektórych zamówień zostanie zapakowana zbyt duża ilość, a do innych zbyt mała. Powodowało to zmiany w planowaniu produkcji w ostatniej chwili, aby uniknąć problemów z dostawą. Dodatkowe zmiany w cyklach pakowania i małe, korygujące cykle odlewania powodowały niepotrzebne koszty. W pewnym momencie zaczęliśmy przeprowadzać codzienne inwentaryzacje w magazynie buforowym, aby tego uniknąć, co pochłaniało wiele godzin pracy”.
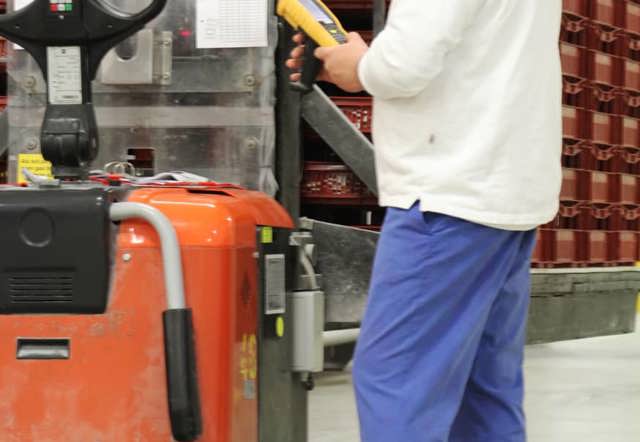
Inwestycje w sprzęt i oprogramowanie
Firma Astra Sweets zainwestowała w cztery systemy ważące z WiFi, dwa RCS Hy-Q na podwójnych w?zkach podnosz?cych i dwa RPW EL na elektrycznych w?zkach paletowych.
Jak to działa?
produkcyjnych musiały być ważone. Rozważano kilka opcji: wbudowanie systemów ważących w linie produkcyjne okazało się kosztowne, a ważenie na wadze podłogowej czasochłonne i nie zawsze bezpieczne ze względu na logistyczne wąskie gardła w ruchu wewnętrznym. Patrick Peeters miał doświadczenie z RAVAS u poprzedniego pracodawcy i zaproponował mobilne ważenie na wózkach magazynowych, które zajmują się transportem wewnętrznym z linii produkcyjnych do magazynu pośredniego. Stefan Verbeken: „Okazało się to najbardziej wydajnym i opłacalnym rozwiązaniem”.
Złożono wniosek inwestycyjny wraz z analizą kosztów i korzyści. Koszty obejmowały cztery systemy ważące, ale także wymianę dwóch starszych wózków, ponieważ według firmy Astra Sweets wbudowanie systemu ważącego w wózki, które miały przed sobą tylko kilka lat użytkowania, byłoby zniszczeniem kapitału. Do tego dochodził koszt modyfikacji oprogramowania Objective, które steruje liniami produkcyjnymi. Korzyści znacznie przewyższały koszty. Natychmiast zaoszczędzono pół etatu na codziennych kontrolach magazynowych i wszelkiego rodzaju poprawkach w pakowaniu. Do tego dochodzi pakowanie zgodnie z zamówieniem, mniej pozostałości i odpadów oraz mniej poprawkowych serii odlewów.
Patrick Peeters opisuje obecny proces: „Obecnie mamy cztery wózki z systemami ważącymi. Zarówno system ważący, jak i ręczny terminal na wózku komunikują się poprzez naszą sieć WLAN z Objective. Gdy półprodukt schodzi z linii produkcyjnej, jest natychmiast ważony na wózku. Operator uruchamia protokół na swoim urządzeniu przenośnym: wprowadza numer linii produkcyjnej i artykuł, którego dotyczy. Następnie uruchamia program Objective, aby zażądać masy z systemu ważącego na wózku, dzięki czemu zestaw danych jest kompletny. Z urządzenia przenośnego drukowana jest etykieta z kodem kreskowym, a paleta trafia do magazynu pośredniego”.
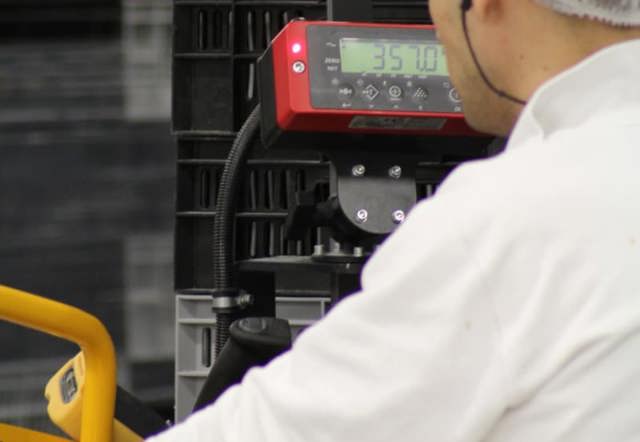
Stefan Verbeken, Manager Planning & Material Supply
„W pewnym momencie zaczęliśmy przeprowadzać codzienne inwentaryzacje, aby rozwiązać ten problem. Kosztowało nas to siłę roboczą, którą mogliśmy wykorzystać w innych, bardziej dochodowych obszarach. Dzięki mobilnym wagom RAVAS generujemy teraz rzeczywiste dane i możemy zarządzać na podstawie wskaźników KPI. Pozwoliło to na natychmiastowe oszczędności, a inwestycja w systemy ważące zwróciła się w krótkim czasie”.
Wyniki
Patrick Peeters: „Zaletą integracji systemów ważących z Objective jest to, że możemy teraz porównywać linie i sprawdzać wyniki systemów ważących. Miesięcznie mamy tylko 50 kg korekt, co jest wartością niezwykle niską w porównaniu z naszym miesięcznym tonażem”.
Stefan Verbeken: „Dane są przesyłane z Objective do SAP. Teraz dysponujemy rzeczywistymi danymi po zakończeniu produkcji. Możemy również przeprowadzać analizy wydajności poszczególnych produktów i na tej podstawie optymalizować procesy. Możemy kierować się wskaźnikami KPI. Planowanie pakowania można teraz znacznie lepiej dostosować do potrzeb klienta. Dzięki mobilnym systemom ważącym RAVAS zrobiliśmy krok naprzód w naszym procesie produkcyjnym”.
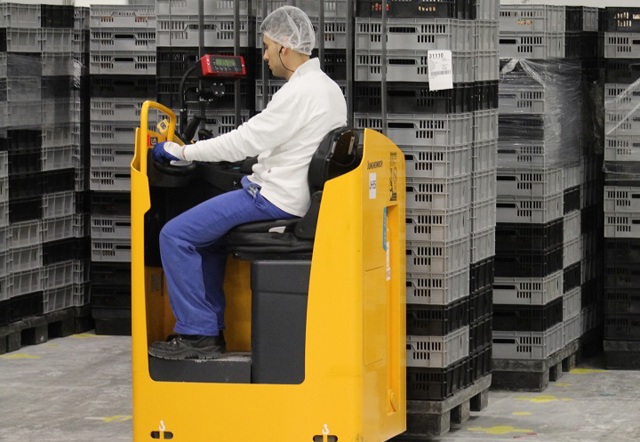
O aplikacji
Kontrola zapasów
Globalne łańcuchy dostaw rozciągające się na różne kontynenty, niewielkie zapasy i dostawy realizowane na zasadzie „just-in-time” sprawiają, że firmy są bardzo podatne na niedobory zapasów. Braki oznaczają przerwy w procesach produkcyjnych, opóźnienia, utratę zaufania klientów. A to wszystko wiąże się z kosztami. Dzięki mobilnej wadze podłączonej do systemu ERP lub WMS można monitorować przepływ materiałów za każdym razem, gdy towary są przemieszczane: towary przychodzące, towary wchodzące do produkcji i wychodzące z produkcji, towary wychodzące. Bez przerywania procesu mobilne wagi pozwalają dokładnie kontrolować stan zapasów, zmniejszyć ich poziom i obniżyć koszty.
Odpowiednie produkty
Do kontroli zapasów
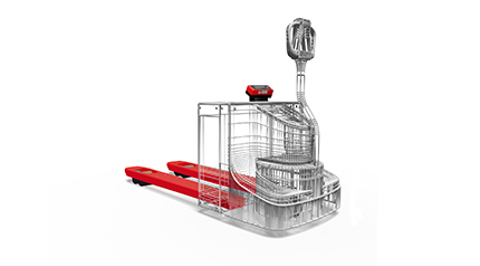
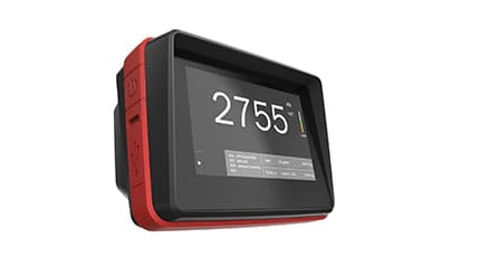
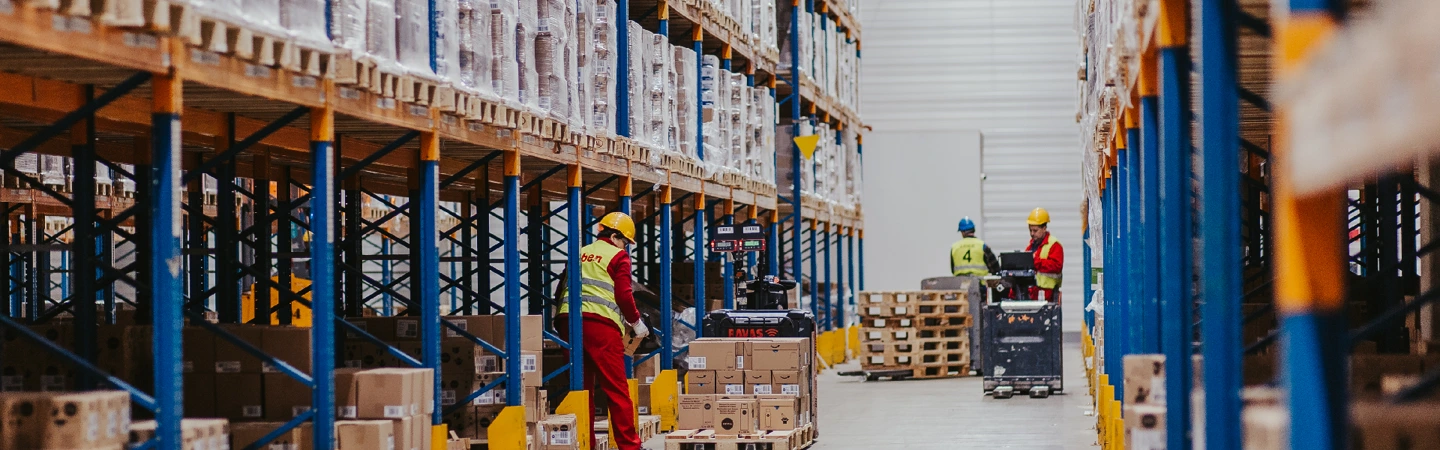