-
- Kundengeschichten
-
ASTRA SWEETS STELLT SOFORTIGE KOSTENEINSPARUNGEN NACH EINFÜHRUNG VON MOBILEN WIEGESYSTEMEN FEST
Aufgrund von einer Vielzahl von Variablen, welche mit der Herstellung von Süßwaren einhergehen, hat Astra Sweets das exakte Gewicht der Produkte, welche von ihren drei Gießanlagen produziert wurden, nicht gekannt. Abweichungen im Puffervorrat der Halbfertigwaren führten zu Überschüssen im Material, Lieferverzögerungen und zusätzlichen Korrekturen in der Produktion. Nun wurden mobile Wiegesysteme von RAVAS an den Staplern angebracht, welche die Süßwaren von den Anlagen zu den Warenhäusern transportieren, und die akkuraten Produktionsgewichte mithilfe des ERP Systems über das drahtlose Netzwerk des Unternehmens übertragen können.
Süßigkeiten aus Turnhout
Baiser, Weingummis, Colaflaschen, Lakritz, Marshmallows, Pfefferminzbonbons: alles Produkte, die Astra Sweets fertigt. Im Hauptwerk in Turnhout stellt das belgische Unternehmen 300 verschiedene Sorten von Süßwaren her. All diese Süßigkeiten werden unter dem eigenen Markennamen an Supermärkte, Drogerien, Tankstellen und Großhändler oder als Hausmarken an eine Vielzahl von Hauptkunden und den internationalen Markt vertrieben.
Während einer Tour durch die Astra Sweets Fertigungsanlage sieht man ständig farbige Süßwaren aus den Anlagen strömen, Roboter, die endlose Tabletts an Süßigkeiten stapeln, und Stapler, die diese in die Pufferlager fahren. Patrick Peeters, Key User der Fertigung, erklärt, wie die Dinge laufen: „Unsere Süßigkeiten fließen in stärkehaltige Gussformen und je nach Art werden sie dann in den Trockenraum oder das Kühllager gebracht. Nach 36 Stunden wird eine Oberflächenbehandlung aufgetragen: aus Öl, Zucker oder Säure. Die halbfertigen Produkte fließen dann auf Tabletts mit je 9 bis 13 kg Süßigkeiten, welche gestapelt und in das Pufferlager transportiert werden. Nach einer Akklimatisierung werden die Süßigkeiten dann nach Kundenbestellung abgepackt.“
Korrekturen in der Produktion und Verpackung führten zu unnötigen Kosten
Die Verwaltung des Pufferlagers ließ Raum für Verbesserungen, sagt Stefan Verbeken, Planungs- und Materialversorgungs-Manager bei Astra Sweets. „Wir fertigen an drei Gießanlagen. Jeder Fertigungsprozess hat Anlaufverluste. Nimmt man hierzu Fehler während der Produktion kann man erkennen, wie signifikant die tatsächliche Produktion von der erwarteten, theoretischen Produktion abweichen kann. Wir kannten natürlich den Rohmaterialeinsatz, konnten aber den exakten Ertrag am Ende der Fertigung nicht messen. Daher konnten wir nicht sicher sein, wie viel Halbfertigprodukt im Pufferlager auf Lager war. Die Unterschiede zwischen den Zahlen im ERP und denen im Warenhaus lagen bei mehreren Tonnen, je nach Größe des Produktionslaufes.“
Die Ungewissheiten bezüglich des gefertigten Puffers an Halbfertigprodukt führten zu Ineffizienz und zusätzlichen Kosten. Um Wechsel zwischen den Produkten auf einem Minimum zu halten werden alle Bestellung, z.B. für Colaflaschen, zusammengenommen und während eines einzelnen Produktionslaufes gefertigt und in das Pufferlager transportiert. „Falls ein Halbfertigprodukt für mehrere Bestellungen geplant wurde, hat dies auf dem theoretischen Ertrag basiert, wodurch das Risiko bestand, dass für einige Bestellungen zu viel und für andere zu wenig abgepackt wurde. Das hat zu kurzfristigen Änderungen für die Fertigung geführt, um Probleme beim Versand zu vermeiden. Zusätzliche Wechsel während der Verpackung und Korrekturgussläufe in geringem Maße erhöhten unnötigerweise die Kosten. Eine Zeit lang haben wir tägliche Inventurprüfungen durchgeführt um dem Problem entgegenzuwirken, wofür wir viele Arbeitsstunden aufgebracht haben.“
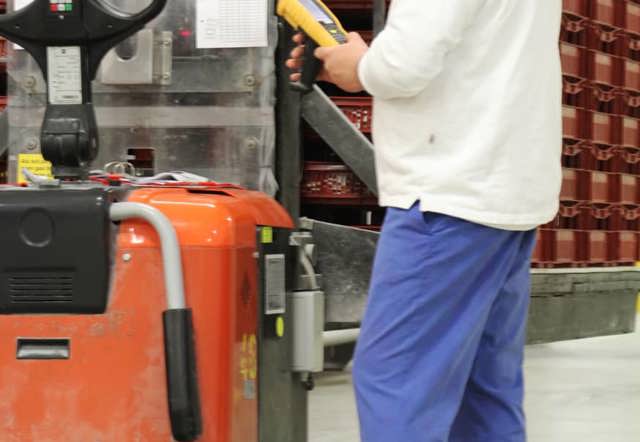
“Eine Zeit lang haben wir tägliche Inventurprüfungen durchgeführt, um dem Problem entgegenzuwirken. Das hat uns Arbeitskraft gekostet, die wir profitabel anderweitig hätten nutzen können. Mithilfe des RAVAS Wiegesystems generieren wir nun tatsächliche Zahlen und können Leistungskennzahlen verwalten. Wir haben sofort Kosteneinsparungen festgestellt und die Investition in die Wiegesysteme hat sich in kurzer Zeit amortisiert.“
- Stefan Verbeken, Planungs- und Materialversorgungs-Manager, Astra Sweets
Der Schlüssel zur Verbesserung: Mobil Wiegen
Ein Projekt zur Verbesserung wurde gestartet: Jegliche gefertigten Süßwaren sollten gewogen werden. Hierfür wurden verschiedene Möglichkeiten betrachtet: Wiegesysteme in die Fertigungsanlage einzubauen erwies sich als teuer, das Wiegen mithilfe von Bodenwaagen als zeitintensiv und möglicherweise unsicher aufgrund von logistischen Engpässen im Warenhausverkehr. Patrick Peeters hatte Erfahrung mit RAVAS bei einem ehemaligen Arbeitgeber und schlug ein mobiles Wiegen auf den Staplern während des Transports von der Anlage zum Pufferlager vor. Stefan Verbeken: „Dieser Vorschlag erwies sich als die effizienteste Lösung, auch bezüglich der Kosten.“
Ein Investitionsantrag wurde eingereicht, belegt mit einer Kosten/Nutzen Analyse. „Die vier Wiegesysteme kosteten uns circa 16.000 Euro, allerdings mussten wir auch zwei ältere Yale Stapler ersetzen, da es eine Verschwendung gewesen wäre, die Wiegesysteme in Stapler einzubauen, welche nur noch einige Jahre in ihrer Nutzungsdauer hatten. Zusätzlich 3.000 Euro für Anpassungen an Objective, der Software, welche die Produktanlage steuert, und wir erreichten 55.000 Euro für unsere Erstinvestition. Der Nutzen überwiegte klar die Kosten. Allein durch tägliche Inventurprüfungen und Verpackungskorrekturen sparten wir sofort die Hälfte unserer Vollzeitäquivalenz. Zusätzlich hierzu kamen das Verpacken der Korrekturfertigung, ein geringerer Überschuss an Rohmaterial und weniger Korrekturgussläufe. Eine Zustimmung kam und Patrick Peeters machte sich mit der IT und anderen beteiligten Abteilungen an die Arbeit.“
Patrick Peeters beschreibt den hieraus resultierenden Produktionslauf: „Wir haben nun vier Stapler mit Wiegesystemen. Sowohl die Waage als auch das Handgerät im Stapler verständigen sich mit Objective über unser drahtloses Netzwerk. Sobald das Halbfertigprodukt am Ende der Fertigung ankommt, wird es sofort gewogen. Der Bediener startet das Protokoll auf seinem Handgerät: Er gibt die Nummer der Fertigungsanlage ein und den Referenzartikel und steuert Objective dazu an, das Gewicht des Produktes per Waage zu ermitteln. Das vervollständigt dann den Datensatz. Vom Handgerät wird ein Barcode-Etikett gedruckt und die Palette wird zum Pufferlager transportiert.“
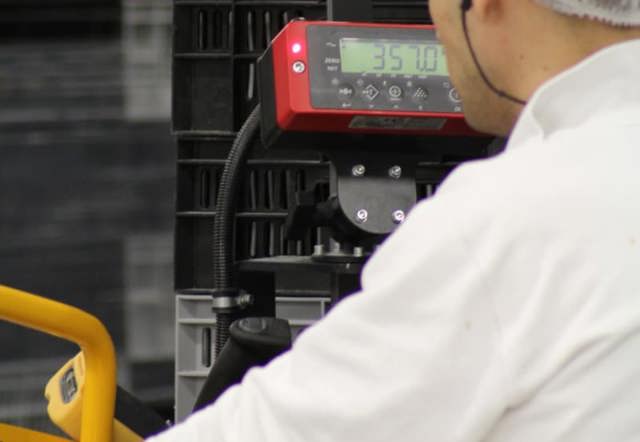
Süße Vorteile
“Auf zwei der drei Produktionsanlagen ist die Integration der mobilen Wiegesysteme in Objective abgeschlossen, die Dritte wird bald folgen“, sagt Patrick. „Das Gute hierbei ist, dass wir nun die Anlagen vergleichen und die Ergebnisse des Wiegesystems sehen können: Bei den zwei bereits integrierten Anlagen haben wir nur noch 50 kg Korrektur pro Monat, was eine extrem geringe Menge ist, verglichen mit unserer monatlichen Produktion in Tonnen. Bei der dritten Anlage haben wir noch tägliche Nachbereitungen und Korrekturen. Wäre dies nicht der Fall, hätten wir Unterschiede von bis zu 10 Tonnen monatlich. RAVAS hilft uns, tägliche Korrekturen auf einem Minimum zu halten.“
Stefan Verbeken: “Von Objective aus werden die Daten in SAP importiert. Wir haben nun tatsächliche Zahlen nach dem Abschluss, können Ertragsanalysen pro Produkt durchführen und von dort aus optimieren. Wir können nach Leistungskennzahlen steuern. Die Planung der Verpackung kann auf dem Bedarf der Kunden angepasst werden. Mit dem RAVAS mobilen Wiegesystem haben wir einen Schritt vorwärts in unserem Fertigungsprozess gemacht.“
FIRMA
Astra Sweets
STANDORT
Turnhout, Belgium
ANWENDUNG
Stock control
Stock control
Mit globalen Lieferketten, die sich über Kontinente ausstrecken, mit kleinen Vorräten und just-in-time-Lieferungen, sind Unternehmen sehr empfindlich geworden für Vorratsmängel. Mängel bedeutet unterbrochene Produktionsprozesse, Lieferverzögerungen, Verlust von Vertrauen der Kunden und die haben alle ihre Kosten. Mit einer mobilen Waage, verbunden mit Ihrem ERP- oder WMS-System, werden Materialflüsse überwacht, jedes Mal wenn Waren gewogen werden: bei Wareneingang, Waren-in, und -aus Produktion, Warenausgang. Ohne Unterbrechung des Prozesses, erlauben mobile Waagen sie Ihre Lager genau zu steuern, Lagerbestände zu reduzieren und Kosten zu senken.