Doces de Turnhout
Merengues, balas de goma (inclusive em forma de garrafinhas de refrigerante), doces de alcaçuz, marshmallows, balas de hortelã: todos esses são produtos que a Astra Sweets fabrica. Em sua fábrica principal em Turnhout, a empresa belga produz 300 tipos diferentes de doces. Todos esses produtos de confeitaria são distribuídos com sua própria marca em supermercados, farmácias, postos de gasolina e atacadistas, ou com rótulo particular a uma série de grandes clientes na Bélgica e no exterior.
Em uma visita à fábrica de produção da Astra Sweets, vê-se doces vivamente coloridos jorrando de máquinas, bandejas de doces sem fim sendo empilhadas por robôs, e caminhões levando os doces para o depósito de segurança. Patrick Peeters, da Produção para o Usuário Principal, explica como as coisas funcionam: “Nosso doce é despejado em moldes de goma. Dependendo do tipo de doce, vai para uma sala de secagem ou para uma câmara frigorífica. Após 36 horas um acabamento é aplicado à superfície, utilizando óleo, açúcar ou ácido. O produto semifinalizado então é despejado em bandejas de 9 a 13 kg de doce cada, que são empilhadas em uma plataforma de carga e transportadas para o depósito de segurança. Após a aclimação, os doces são então empacotados de acordo com os pedidos dos clientes.”
Produção corretiva e empacotamento geram custos adicionais desnecessários
A gestão de estoque de segurança deixou espaço para a melhoria, diz Stefan Verbeken, Gerente de Planejamento e Fornecimento de Materiais da Astra Sweets. “Nós produzimos em três linhas de moldagem. Todo processo de produção tem suas perdas iniciais. Acrescente falhas durante um ciclo e você pode ver por que o resultado real pode ser significativamente diferente do resultado teórico esperado. Claro que conhecíamos a entrada de matéria-prima, mas não podíamos medir a produção exata ao fim da linha. Portanto não podíamos ter certeza de que nenhum produto semifinalizado estava em estoque no depósito de segurança. As discrepâncias entre o estoque em nosso ERP e no estoque em nosso depósito podiam chegar a várias toneladas, dependendo do tamanho do ciclo de produção.”
As incertezas nos estoques de segurança de produto semifinalizado levaram a ineficiência e custos extras. Para manter as mudanças de produtos nas linhas a um mínimo, todos os pedidos de clientes, por exemplo balas de goma em forma de garrafinhas de refrigerante, são agrupados em um único ciclo de produção, produzidos e então transportados para o depósito de segurança. “Se um produto semifinalizado foi planejado para múltiplos pedidos de empacotamento, então isso teve base na produção teórica, com o risco de que em alguns pedidos muito fosse empacotado e em outros, muito pouco. Isso causava mudanças de última hora no planejamento da produção para evitar problemas de entrega. Mudanças adicionais nos ciclos de empacotamento e pequenos ciclos de moldagem corretivos acrescentavam custos desnecessários. Em um momento começamos a fazer inventários diariamente nos depósitos de segurança para evitar isso, gastar um monte de horas de mão de obra.”
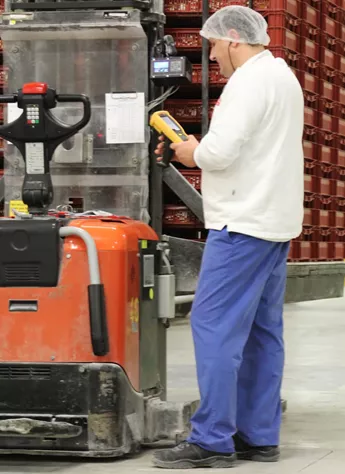
“Em um momento começamos a fazer inventários diariamente para combater o problema. Isso nos custou mão de obra que poderíamos ter usado proveitosamente em outro lugar. Utilizando as balanças móveis RAVAS agora geramos números reais, e podemos administrar com base em KPIs (Principais Indicadores de Desempenho). Isso acarretou uma economia imediata nos custos, o investimento em sistemas de pesagem pagou-se em pouco tempo.”
- Stefan Verbeken, Gerente de Planejamento e Fornecimento de Materiais
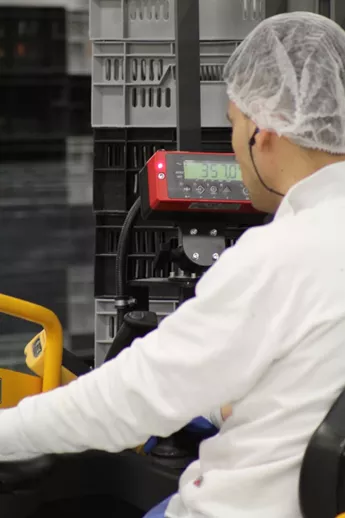
A chave para a melhoria: pesagem móvel
Um projeto de melhoria foi iniciado: todo doce saindo das linhas seria pesado. Diferentes opções foram contempladas: integrar sistemas de pesagem nas linhas de produção mostrou-se caro, pesar em uma balança de chão leva muito tempo e é potencialmente perigoso devido aos congestionamentos logísticos no trânsito do depósito. Patrick Peeters teve uma experiência com a RAVAS em uma empresa na qual trabalhou antes e propôs a pesagem móvel nos caminhões do depósito que realizam o transporte das linhas de produção para o depósito de segurança. Stefan Verbeken: “Essa se mostrou a solução mais eficiente, e também com a melhor relação custo/benefício.”
Uma solicitação de investimento foi feita, comprovada por uma análise de custo/benefício. “Os quatro sistemas de pesagem nos custaram aproximadamente 16.000 euros, mas também tivemos que substituir dois caminhões Yale mais velhos, pois seria um desperdício de capital instalar uma balança em caminhões que tinham apenas alguns anos restantes no seu ciclo de vida. Acrescente 3.000 euros para ajustes ao Objective, o software que gerencia nossas linhas de produção, e acabamos com 55.000 euros como nosso investimento inicial. Os benefícios facilmente superaram os custos. Só nos inventários diários e nas correções de empacotamento economizamos metade do ETI (Equivalente do Tempo Integral) imediatamente. Acrescente a isso: empacotamento na ordem correta, menos material residual, e menos ciclos corretivos de moldagem. A aprovação veio e Patrick Peeters colocou o projeto em prática com o TI e outros departamentos envolvidos.”
Patrick Peeters descreve o processo de produção resultante: “Agora temos quatro caminhões com uma balança de pesagem. Tanto a balança como o computador de mão no caminhão se comunicam o Objective por nossa rede WLAN. Quando o produto semifinalizado sai da linha, é imediatamente pesado. O operador inicia o protocolo em seu computador de mão: ele insere o número da linha de produção e a referência do artigo, e então aciona o Objective para perguntar o peso à balança. Isso completa o conjunto de dados. Do computador de mão é impresso um rótulo com o código de barras e a plataforma de carga é transportada ao depósito de segurança.”
Doces benefícios
“Em duas das três linhas de produção a integração dos sistemas de pesagem móveis no Objective já está completada, na terceira linha também logo será”, diz Patrick. “O bom disso é que podemos comparar as linhas e ver os resultados dos sistemas de pesagem: nas duas linhas integradas agora ficamos com apenas 50 kg de correção por mês, o que é uma quantidade extremamente pequena comparada com nossa tonelagem mensal. Na terceira linha ainda acompanhamos e fazemos correções diariamente. Se não fizéssemos isso, teríamos diferenças de até 10 toneladas todos os meses. A RAVAS está nos ajudando a limitar as correções diárias a um mínimo.”
Stefan Verbeken: “Do Objective os dados são importados no SAP (Sistemas, Aplicações e Produtos). Agora temos números reais após o acabamento, podemos realizar análises de produção por produto e a partir daí otimizar. Podemos administrar com base em KPIs. O planejamento de empacotamento pode ser ajustado às necessidades do cliente. Com os sistemas de pesagem móvel RAVAS demos um passo à frente em nosso processo de produção.”
COMPANY
Astra Sweets
LOCATION
Turnhout, Belgium
APPLICATION
Controlo de stock
Controlo de stock
Com uma cadeia de abastecimento que se estende através de continentes, com stock reduzidos e entregas just-in-time, as empresas tornaram-se muito vulneráveis a ruturas de stock. Ruturas significam interrupções nos processos de produção, atrasos, perda de confiança do cliente. E tudo isto tem um custo. Com uma balança móvel, conectada ao seu sistema ERP ou WMS, fluxos de materiais podem ser monitorizados sempre que os bens são movimentados: entrada de bens, bens que entram ou saem da produção, saída de bens. Sem interromper o processo, balanças móveis permitem-lhe um controlo de stock mais exato, reduzindo níveis de stock com menores custos.