-
- Storie di clienti
-
ASTRA SWEETS REALIZZA RISPARMI IMMEDIATI SUI COSTI PESANDO LA PRODUZIONE
A causa del numero di variabili nella produzione dei dolciumi, Astra Sweets non conosceva esattamente l’esatto peso delle tre linee di produzione. Le discrepanze nella scorta stabilizzatrice dei prodotti semi-lavorati hanno provocato resti di materiali, ritardi e fasi di produzione aggiuntive e correttive. Adesso i sistemi di pesatura mobile RAVAS sono installati sui carrelli che trasportano i dolciumi dalle linee al magazzino e pesi accurati della produzione sono comunicati con il sistema ERP al provider mediante rete wireless.
Dolciumi da Turnhout
Meringues, wine gums, cola bottles, liquorice drops, marshmallows, peppermint: those are all products that Astra Sweets manufactures. At its main plant in Turnhout, the Belgian company produces 300 different kinds of sweets. All this confectionery is distributed under its own brand name to supermarkets, drug stores, petrol stations and wholesalers, or under private label to a range of major customers in Belgium and abroad.
On a tour through the Astra Sweets production plant, one sees lively colored sweets pouring out of machines, endless trays of sweets being stacked by robots, and trucks driving the candy to the buffer warehouse. Patrick Peeters, Key User Production, explains how things work: “Our candy is poured into starch casting molds. Depending on the type of sweets, the candy then either goes to a drying room, or to cold storage. After 36 hours a surface finishing is applied, using oil, sugar or acid. The semi-finished product then flows into trays of 9 to 13 kg candy each, which are stacked on a pallet and transported to the buffer warehouse. After acclimatization the sweets are then packaged according to customer orders.”
Le fasi correttive della produzione e d’imballaggio aggiungono costi inutili
La gestione della scorta stabilizzatrice deve ancora migliorare, dice Stefan Verbeken, Manager Planning and Material Supply di Astra Sweets. “Produciamo su tre linee. Ogni processo di produzione ha le sue perdite nell’avviamento. Aggiungete avarie durante una fase e osservate il motivo per il quale il vero output può essere molto diverso dalle aspettative, output teoretico. Naturalmente conosciamo l’input delle materie prime ma non possiamo misurare l’esatto rendimento alla fine della linea. Non siamo quindi certi sulla quantità di prodotti semi-lavorati che si trova nello stock del magazzino di scorta. Le discrepanze tra lo stock nel nostro ERP e lo stock nel nostro magazzino possono essere di molte tonnellate, a seconda delle quantità della fase di produzione”.
Le incertezze nella scorta stabilizzatrice dei prodotti semi-lavorati creano inefficienze e costi aggiuntivi. Per mantenere al minimo i cambiamenti del prodotto nelle linee, tutti gli ordini dei consumatori per esempio di bottigliette alla coca cola, sono raggruppati in una sola fase di produzione, sono prodotti e trasportati nel magazzino della scorta. “Se un prodotto semi-lavorato era programmato per degli ordini con imballaggi multipli, era quindi basato sul rendimento teoretico con il rischio che per alcuni ordini era stato imballato troppo e per altri troppo poco. Questo provocava dei cambiamenti all’ultimo minuto nella pianificazione della produzione per evitare problem nella consegna. I cambiamenti extra nelle fasi dell’imballaggio, le fasi di correzione aggiungono costi inutile Ad un certo punto, dovevamo eseguire tutti i giorni l’inventario nel magazzino della scorta per evitarlo, spendendo molte ore di lavoro”.
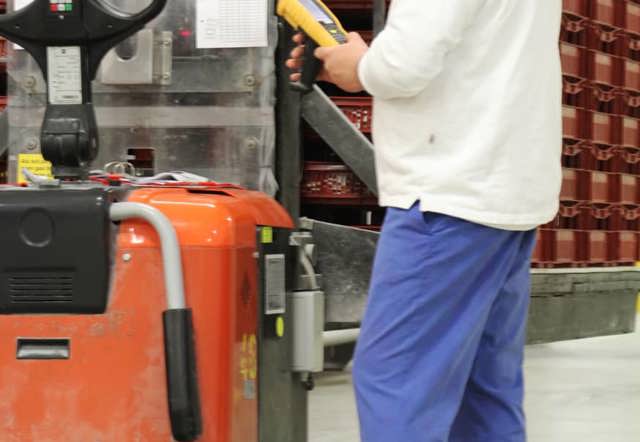
“Ad un certo punto, dovevamo eseguire tutti i giorni l’inventario per affrontare il problema. Questo processo richiedeva forza lavoro che potevamo usare in modo più efficiente in altre mansioni. Usando i sistemi RAVAS, possiamo creare delle vere cifre e gestire con i KPI. Realizziamo risparmi immediati sui costi, l’investimento sui sistemi di pesatura è stato riguadagnato in breve tempo.”
- Stefan Verbeken, Manager Planning & Material Supply, Astra Sweets
La chiave del miglioramento: pesatura mobile
È iniziato un progetto di miglioramento: tutti i dolciumi che escono dalle linee devono essere pesati. Sono state considerate varie opzioni: sistemi di pesatura integrati nelle linee di produzione si sono rivelati molto costosi, la pesatura su una pesatrice nella fabbrica durava troppo e era forse pericolosa a causa dei problemi logistici del traffico dentro il magazzino. Patrick Peeters ha avuto delle esperienze con RAVAS presso un ex datore di lavoro e ha proposto la pesatura mobile, con carrelli nel magazzino che eseguono il trasporto dalle linee di produzione al magazzino della scorta. Stefan Verbeken: “Questa si è rivelata la soluzione più efficiente anche in termini di costi”.
È stata presentata una richiesta d’investimento, convalidata da un’analisi costi/vantaggi. “I quattro sistemi di pesatura ci costano circa 16.000 Euro, ma dovevamo anche sostituire due vecchi carrelli Yale dato che sarebbe stato uno spreco di capitali costruire una pesatrice sui carrelli ai quali rimanevano solo pochi anni di durata. Aggiungendo 3.000 Euro per gli adattamenti con Objective, il software che gestisce le nostre linee di produzione, finivamo con 55.000 Euro di investimento iniziale. I vantaggi superavano molto i costi. Solo per gli inventari giornalieri e le correzioni sull’imballaggio abbiamo risparmiato immediatamente metà FTE. Aggiungete anche questo: l’imballaggio nel giusto ordine, meno resti di materiali e meno fasi correttive. È arrivata l’approvazione e Patrick Peeters ha iniziato a lavorare con l’IT e a coinvolgere altri dipartimenti”.
Patrick Peeters descrive il processo di produzione che hanno ottenuto: “Adesso abbiamo quattro carrelli con una pesatrice. Sia la pesatrice e il sistema sul carrello comunicano con Objective sulla nostra rete WLAN. Quando il prodotto semi-lavorato esce dalla linea, è immediatamente pesato. L’operatore inizia il protocollo sul suo sistema: inserisce il numero della linea di produzione e il riferimento dell’articolo e attiva Objective per interrogare la bilancia per il peso. Questo completa il set dei dati. Dal sistema, un’etichetta con il codice a barre è stampata e il pallet è trasportato nel magazzino della scorta”.
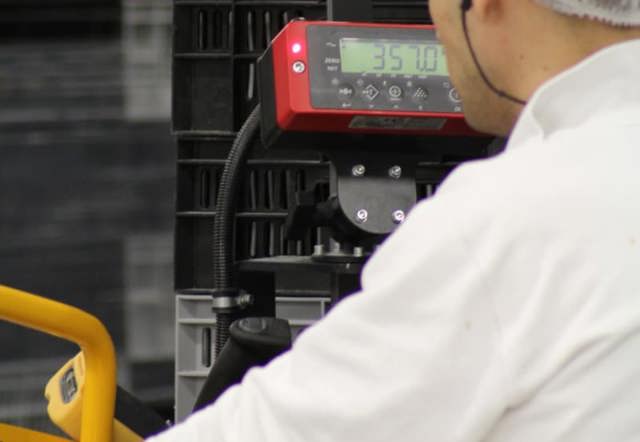
Vantaggi Sweet
“Su due delle tre linee di produzione, l’integrazione dei sistemi di pesatura mobile nel Objective è di nuovo completa, per la terza linea inizierà tra poco”, dice Patrick. “Il bello è che possiamo paragonare le linee e vedere i risultati dei sistemi di pesatura: sulle due linee integrate, ci rimangono solo 50 kg di correzione al mese che è una quantità veramente bassa rispetto al nostro tonnellaggio mensile. Sulla terza linea, eseguiamo ancora il follow-up e le correzioni mensili. Se non l’avessimo fatto, avremmo delle differenze fino a 10 tonnellate su base mensile. RAVAS ci sta aiutando a limitare al minimo le correzioni giornaliere.”
Stefan Verbeken: ”Da Objective, i dati sono importati nel SAP. Adesso abbiamo delle cifre reali dopo la finitura, possiamo eseguire delle analisi sul rendimento per ogni prodotto e quindi ottimizzare. Possiamo gestire con i KPI. La pianificazione dell’imballaggio può essere adattata alle necessità del cliente. Con i sistemi di pesatura mobile RAVAS, abbiamo fatto un passo in avanti nel nostro processo di produzione”.
AZIENDA
Astra Sweets
POSIZIONE
Turnhout, Belgium
APPLICATION
Gestione magazzino
Gestione magazzino
Con catene di fornitura globali che si estendono attraverso i continenti, con piccole stock e consegne just-in-time, le aziende sono diventate molto vulnerabili a carenze di stock. Carenze significano processi produttivi interrotti, ritardi, perdita di fiducia dei clienti. E tutti sono dotati di un costo. Con una bilancia mobile, collegato al sistema ERP o WMS, i flussi di materiali possono essere monitorati ogni volta che le merci sono trasferite: merce in entrata, le merci in entrata e in uscita di produzione, merce in uscita. Senza interrompere il processo, bilancie mobili consentono di controllare con precisione il vostro magazzino, riducendo i livelli di stock e abbassando costi.