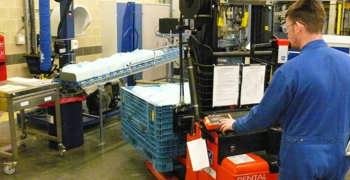
-
- Customer Stories
-
3M CHECKS HIGH-VALUE OUTBOUND BATCHES BY WEIGHT
At a stone’s throw of the Port of Antwerp, 3M produces semi-finished product and raw materials for a multitude of specialised products, such as foils for the aerospace industry or surgical tape for medical applications. Since these substances often represent a high value, deliveries are carefully checked by weight. This is done by means of RAVAS scales on stackers and hand pallet trucks.
From sandpaper to nanotechnology in a hundred years
In the year 1903 the Minnesota Mining & Manufacturing company, soon to become 3M, first opened its gates. In the following one hundred years the company evolved from the production of sandpaper to the use of nanotechnologies. Nowadays 3M produces a great variety of specialized materials, from structural adhesive films for the aerospace industry, to specialized dressings for wound care, or cooling fluids for electronics. Oh, and Scotch tape and Post-its…
In Belgium, in the Antwerp Port area, in the shadow of surrounding heavy industries, 3M Specialty Materials is located. The Antwerp site produces mainly semi-finished product for other 3M production sites and raw materials for client companies. Thus 3M Specialty Materials produces adhesives for the production of surgical tapes, but also manufactures the coating that makes GORE-TEX clothing watertight.
Expensive product demands weight checks per 100 gram
Many specialist products are built from common materials that are treated with an advanced additive. Think of rubber that is adapted to resist extreme temperatures and pressures. Such additives are often quite costly, which turns a simple weight check into a demanding process: 1,000 liters of product in an IBC container is weighed in 100 gram increments. And in order to make the process as efficient as possible, 3M weighs mobile: on the material handling equipment that transports the IBC’s and boxes.
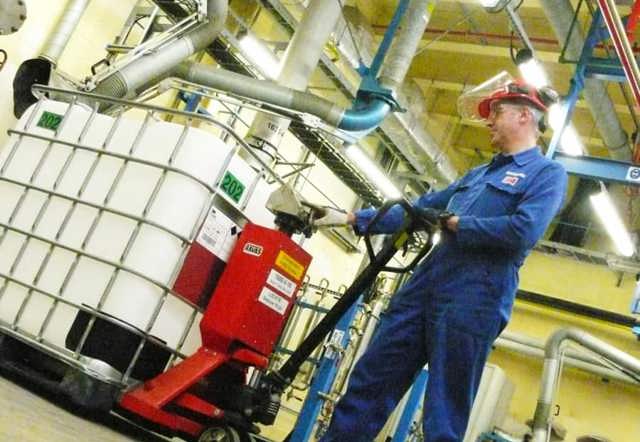
”With iForks on the stackers, we have improved mobility and execution speed in our weight checks. The process has become considerably more efficient.”
- GEERT VAN EYKEN, SUPERVISOR ADVANCED MATERIALS DIVISION
Stackers weigh boxes, Proline pallet trucks weigh IBC's
At the end of a production line, 12kg packages slide off a roller conveyor. They are packed in large plastic crates, 50 packages in each crate. Special Toyota stackers with reach mast not only stack the boxes for shipping, but also weigh them in order to verify that the delivery contains the correct amount of product. To this end the stackers are equipped with legal for trade iForks scales. The iForks display shows the exact weight of the crate on the forks.
The stackers also weigh rest materials that are by-products of the production process. These materials can be re-used in production and are weighed for stock management before they are transported back to the warehouse.
In a building on the other side of the 3M site inert fluids for cooling and cleaning of electronics are produced. These “engineered fluids” represent a high value, which is why the weight of the IBC containers in which these fluids are stored, is meticulously controlled. RAVAS ProLine pallet truck scales, delivering a high accuracy thanks to the patented FlexBolts in the forks, are used to transport and weigh the IBC’s. And since certain production areas are classified hazardous because of the use of highly flammable substances, part of the pallet truck scale fleet is certified ATEX explosion proof.
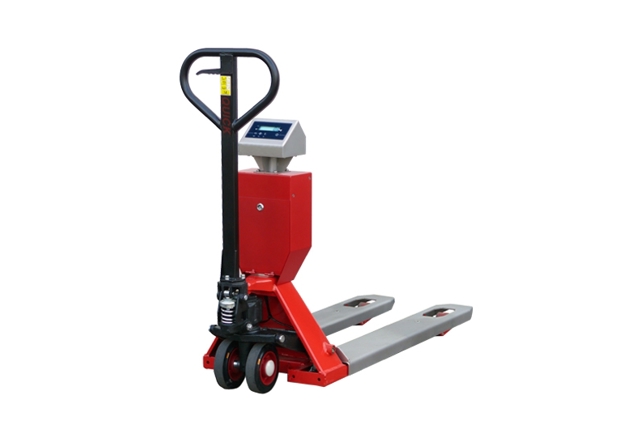
Maintenance contracts guarantee quality and accuracy
At 3M the complete fleet of mobile weighing systems is covered by maintenance contracts. Once a year a RAVAS calibration truck, with certified weights on board, rolls onto the 3M site. Over a period of three days all mobile scales are serviced, re-calibrated and re-certified. Thus the accuracy of the systems is guaranteed, the service life optimized.
COMPANY
3M
LOCATION
Zwijndrecht, Belgium
APPLICATION
Dosing and mixing
Dosing and mixing
When producing batches of semi finished or finished product, the aim is to correctly mix the different ingredients and components. Amounts and proportions determine the quality of the product. A mobile scale helps you to produce cheaper, safer and more efficient. It also generates the information you need for quality control and tracking and tracing procedures. The scale is brought to the components: on a hand pallet truck scale the mixing vessel is driven from one ingredient to the next and components are dosed straight from their container. The risk of damages and product loss is greatly reduced.